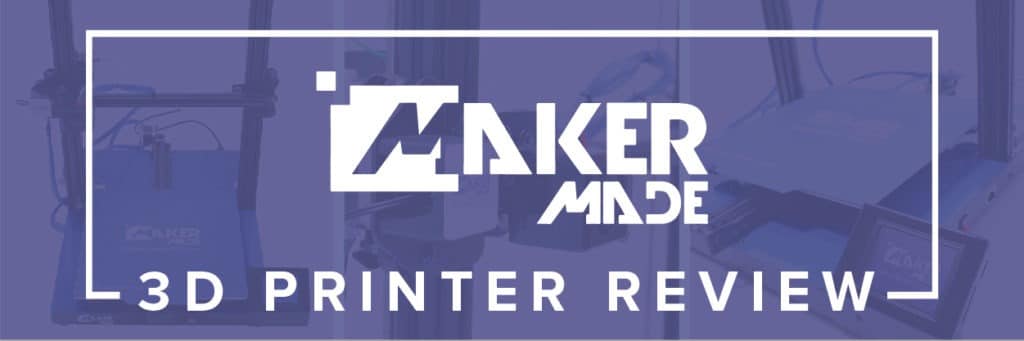
3D Printer In-Depth Overview with Jacob
We’ve been so excited about getting our 3D printer out to you all and knew you’d have a LOT of questions about our set up.
Jacob has been more seriously designing and testing high-temperature printers for the last 3 years to include liquid-cooled hotends, steppers, boards, >400C hotends, heated chambers, and the like. He currently owns 5 off the shelf printers from various manufacturers and typically has 2-3 printers in various states of functionality to test ideas and new products.
We sent a model to Jacob to test for us he gave us a great rundown on the details of the machine and his thoughts. You can read his detailed overview below!
Finally, some free time to talk about the Maker Made maker300 3d printer. I have a pre-production machine, and am very much into the 3d printing ‘scene’ and happy to answer any questions. I have gone through every inch of the machine, so let’s start with what’s included
Packaging
The printer came very well packaged. My delivery driver is Ace Ventura and despite his attempts, everything inside the box was in mint condition. Included was 200G of PLA, enough to get some prints done and ensure everything’s working if you don’t have any on hand
Assembly
Assembly was fairly easy. My pre-production sample didn’t have instructions – but it was easy enough to be printing within an hour or two. It comes mostly assembled, cables have labels when more than one’s poking out a hole so you know where it goes. You’re essentially unpacking, putting in 6 screws, and plugging in ~10 cables before its ready to go.
The Mainboard
The mainboard is a Makerbase MKS Gen L V1.0 board.
The board supports 5 stepper drivers, and came loaded with 4.
X Axis – LV8729
Y Axis – LV8729
Z Axis – LV8729
E0 – 4988
All drivers came with heatsinks and thermal compound pre-applied. The mainboard has a 5015 fan blowing directly over/under the row of drivers to keep them cool
The Z-Axis stepper runs to a separate parallel board, that controls two Z-axis stepper motors.
This board is one of the big pros for me. It’s a well-used form factor and was built to be easy to use and modify. It’s a workhorse of a board, can accommodate a ton of new features if you like to add and tinker as well (bed leveling probes, filament runout sensors, far end endstops, etc). This is in contrast to the cost/feature minimized trend in the printer community where you’re looking at replacing and re-wiring everything if you plan on any upgrades.
The Case
Looking at the case, it’s solid. The steel is thick on the sides and adds to the rigidity of the frame. It has 4 major panels each opened with 4 Phillips screwdrivers. The mainboard sits directly under one panel, and the area for the PI sits to the left allowing for easy access. There are multiple cutouts built-in to allow you to pass cables in/out if needed. The printer has adjustable rubber feet on all 4 sides to eliminate vibrations and stabilize the build platform
The frame’s solid. Easily built to print at 300x300x400 without vibrations or flexing. The uprights are 2040 aluminum V-slot extrusions, and the x-axis is a 2020 aluminum extrusion. Each upright has 2 pre-drilled and tapped holes on the sides that bolt through the case, and one on the bottom to ensure the frame sits very snugly. I bolted the bottom in first to ensure the uprights were pulled all the way down and then bolted in the sides ensuring everything was nice and square
The X-axis
The x-axis is great – it shares the same carriage as the ever-popular Ender 3 and Creality CR-10 series printers. That’s great, for me it meant if I wanted to do any modifications or upgrades I had thousands of pre-modeled solutions and thousands of additional users that could help if I ever got stuck. The belt tension is adjustable by just removing some bolts and pulling it tight, then re-bolting everything. The axis uses 3 v-slow wheels, with 1 eccentric nut to allow for adjusting the tension of the rollers
The Y-axis
The Y-axis is built on a 2040 frame, with 3 pairs of v-wheels, each pair has one side with an eccentric nut for adjusting the tension. The wider frame allows for a more stable bed and is much appreciated. The tension of the belt is adjusted the same as the X-axis, just remove 4 screws and pull the tensioner tight and re-screw it down
The Z-axis
The maker300 came with dual Z motors – tied in parallel so there’s no risk of them really getting out of step. The leadscrews are attached with a flexible coupler to the steppers to keep from binding. The top of the lead screws are not captured with a bearing so it won’t contribute to binding or wobble but are surrounded with a metal piece to ensure they don’t get caught on anything and bent. The Z-axis rides on v-slot wheels and has an eccentric nut to ensure its tight on each side as well. The backlash on my printer was very low as well so all appears well on that front
The Extruder
The extruder is a fairly typical extruder, mine didn’t appear to be a mk10 but was similar. It uses a bowden tube to feet it hotend, and mounts on the left-hand side of the printer – on the X-axis so bowden tube length is kept to a minimum. The case material is plastic
The Hotend
My printer arrived with a mk8 hotend. It is PTFE lined so printing PLA and PETG are easy – and can print material up to ~245C (IMHO) very well. That covers PLA, TPU, metal filled filaments, CF blends, PETG, etc. Nozzle diameter was .4mm and it was brass. The machining on the nozzle was quality, and the bowden tubes were cut cleanly and the hotend was assembled correctly at temperature and had no leaks or other issues
The Build Plate
The build plate looks to be based upon a mk2b 24v heated bed. It’s known to be able to hit over 100C if needed, but it’s topped with a magnetic sheet (So don’t go over 80-85C if you want it to stay super magnetic forever). The build surface is a removable, very flexible buildtak like surface. It did really well in my adhesion tests, and parts came off easily when flexed. It leaves a smooth pattern on the bottom of prints, which I really like.
The First Print
Normally I spend a couple of hours ensuring everything’s square, checking belt tension, adjusting eccentric nuts – but I just plopped this down and started the print right away. The vase I chose ended up great but had some stringing up top (printing too hot). Watertight vases a single layer of plastic thick are a good sign! Since this vase wasn’t meant to be a single layer thick, I clipped off the top and bam – something my girlfriend loves was born
Out of the box – calibration cubes looked good, the extruder was very accurate, the bed and hotend appeared to have been PID tuned, so overall a very positive experience.
This is a VERY solid first, second, third printer for anybody out there looking. For me though, the fun comes in changing things. Luckily for me, this is easy to modify and I’m happy to do a few posts later about how crazy you can make this thing!
Our 3D Printers are available for pre-order NOW in our shop!